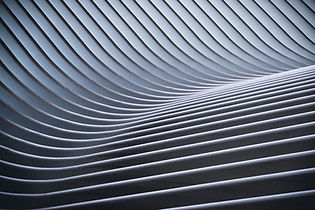
How to Construct a Fishbone Diagram
Develop and agree on a problem statement (effect)
Brainstorm a list of possible causes; remove symptoms and solutions related to the stated effect
Identify major categories of causes (e.g. Man, Machines, Material,Method, Measurement, Environment)
Place each cause in a category (same cause can occur in several categories)
Ask “Why does this happen?” for each cause
Design data collection strategy to verify and prioritize main causes
DMAIC for Lean Six Sigma Projects
-
Define - the business problem ( or opportunity), Team and Scope
-
Measure - the process current state ( as-is) of the problem area
-
Analyze - determine Root Cause of the problem
-
Improve - identify and Choose Best Solution then implement the solution
-
Control - ensure your solution is working. Monitor and Control.
Pareto Analysis
-
The Pareto Principle was first developed in 1906 by Italian economist, Vilfredo Pareto, who observed that 20% of the population owned 80% of the wealth.
-
Also called the 80 : 20 rule.
-
Dr. Joseph M. Juran adapted Pareto's economic observations to business applications.
-
Dr. Juran stated that “80% of Defects in Process Outputs are as a result of 20% of the total Defective Process Inputs



EXAMPLES OF LEAN SIX-SIGMA GREEN BELT COURSE MATERIAL
-
The purpose of Graphing is to:
-
Provide a VISUAL representation of the data
-
Identify potential relationships between the data
-
Indicated the amount of variation in the data
-
Show how data changes over time
For example…
1.Histograms
2.Box Plots ( Box and Whisker plots )
3.Scatter Plots
4.Time Series Plots

•ABC Engine Manufacturing Ltd buys its camshafts for its engines from 2 different suppliers.
•Supplier 1 and Supplier 2
•ABC wants to know what the CAPABILITY is of each supplier to meet its requirements for length of the camshaft.
•The requirements set by ABC are defined by its Specification Limits
LSL = 598 mm
USL = 602 mm
A CAPABILITY STUDY is run in order to investigate.
1.Common Cause Variation
Expected, natural and inherent in every process. Due to random small changes in the process inputs. Small changes in temperature, vibration, wait time or worker energy level are examples. ‘Chronic’ variation
2. Special Cause Variation / Assignable Cause Variation
Unexpected, not part of the process. Often due to external influences out of our control such as accidents, mechanical or electrical failures. ‘Sporadic’ variation. Can be either an ‘Outlier’ or an unusual ‘Pattern or Trend’ in the data. See the ‘Western Electric’ tests for Special Causes.
